I saw the news on Facebook at some point over the weekend that Frank Kozik had died. Frank was one of the undisputed greats of the rock poster business, no doubt. Anyone you talked to in the Austin art world, and I presume well beyond, will attest to that. He was prolific, well-connected and had a strong style that was iconoclastic, ironic, satirical. His aesthetic was perfect for the post-punk and underground music scene that he so heavily influenced. In the early 90’s, Frank became known for his art prints and band posters, but we all have to make a living, and before he really took off, he took work where he could get it, illustrating whatever came up.
Some of that work was t-shirt designs, and I was fortunate to have printed several of those. I forget exactly how we got initially connected, but for a short while in probably early ’89 when he was in between gigs, Frank was actually an employee at the Action Screen Graphics, the shop I managed at the time. It was for just a couple months, but as the shirt design work rolled in after that, he brought it to us. At some point that year, he leased a space that was attached to the side of Action for his poster printing studio, so for a year or so, I saw him pretty much every day.
Frank’s studio was the left part of this building on Toomey Rd, with the overhead Door, and Action was behind it and to the right, through the open doors. Blurry pic is blurry. Not sorry, it’s all I have.
It seems trite when writing something memorial to say that someone was larger-than-life and had an outsized sense of humor that infected everyone around them, but this was true of Frank. His humor was dry and sarcastic, but he could laugh. I was at the pawn shop on S. Lamar one day retrieving a bass guitar (Hey, we were all still recovering from the 80’s and one did what one had to do) when I saw this vinyl LP for sale with the most hilariously bad cover art I’ve almost ever seen, and I snapped it up for a buck and gave it to Frank. He thought it was hilarious, and we had a good laugh. I half-expected bits of it to show up in a poster. My apologies if you were one of the members of Stryken, but man your cover was bad.
I’m not sure if Frank did this Surfers design or not, but I’m pretty certain that we were lucky enough to have printed some butthole Surfers shirts as a result of Frank being around. Gibby came by to press check this design, and I had the singular pleasure of observing him on one of the first cell phones I’d ever seen, cursing out a vendor in LA who refused to duplicate a film they needed to project at a show on grounds of Obscenity.
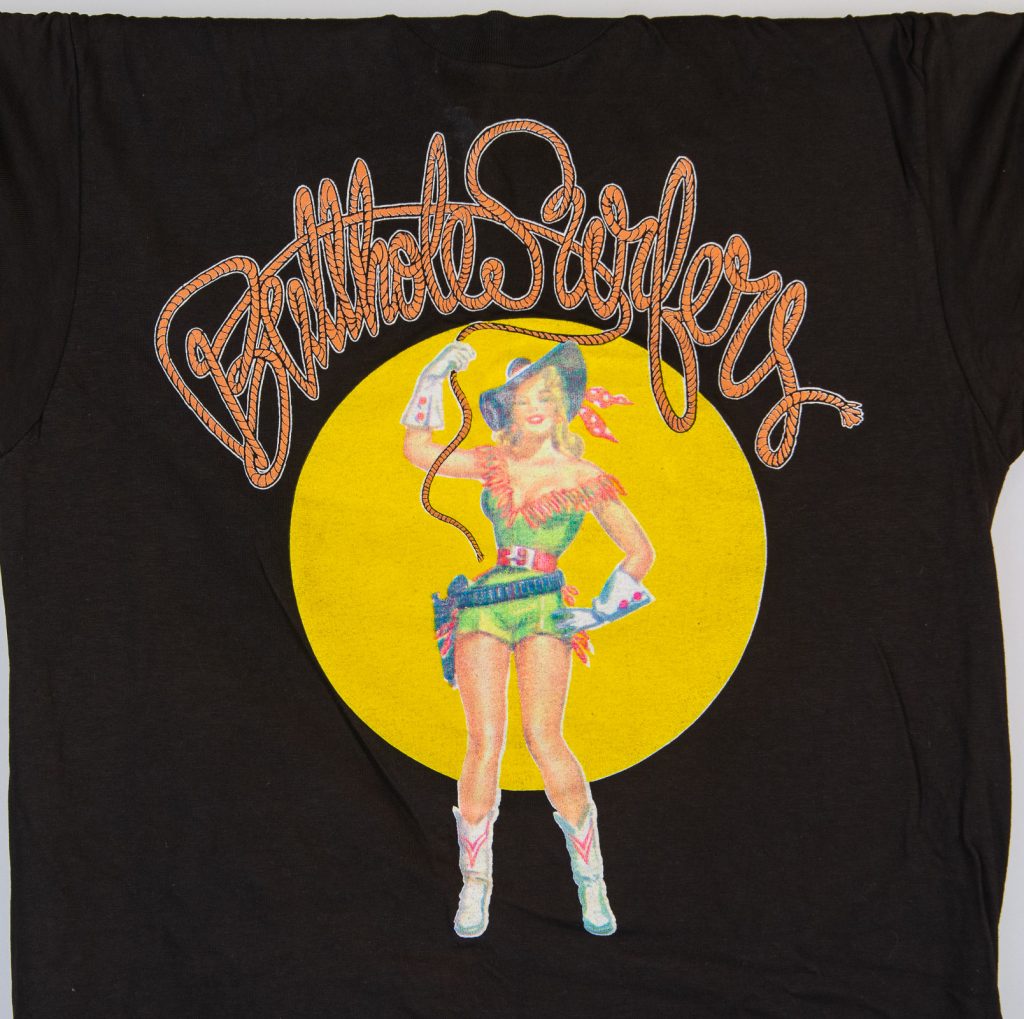
This is a shirt that he drew for, I think, a philosophy club at UT. It used to say something else in the word bubble, but I customized my own shirt by taping that out, and pasting in a line of dialog from one of my favorite cable access shows called From Socrates to Sartre with Thelma Z. Levine. Thelma was a huge Kant fan. In the process of doing that, I spelled Immanuel wrong, Frank noticed it and mocked me mercilessly. Deservedly so. I managed to kind-of fix it with a Zim gun, but alas. That was another aspect of Frank – if you were an idiot, he didn’t have any problem with telling you so. It was usually deserved. My friend Troy Dillinger wrote a pretty nice comment on Frank’s Facebook page to that effect on Monday. I’m not going to try to link it here because that never works, but if you know Troy, look it up.
So we all use computers now, right? I’m a desk jockey for the most part now. I’ve been running graphic design software since the late 90’s and it’s big part of my job to do stuff in Photoshop & Illustrator. Not so much so in 1990, but Frank had gotten his hands on someone’s Amiga, and was working on a Butthole Surfers album cover on it. We had a Windows PC at work with Win 3.1 on it, but it really didn’t interest me much and I never used it. He invited me over though to take a look at this thing, and he showed me some of the cool stuff the graphic design programs, even then, could do for image manipulation. He was really excited and enthusiastic about the potential, and it got me interested, too. Not too much later, I had my first Mac in 1994, and it was off to the races. So in a pretty large way, I have Frank to thank for giving me my first push into the digital age.
All the prints in this post were hand-separated, though. He would have a camera shot done to make a film positive of the line art, then cut amberlith seps with a swivel knife for all the colors. He was amazingly fast at it, too.
Some Youtube links of Kozik interviews: